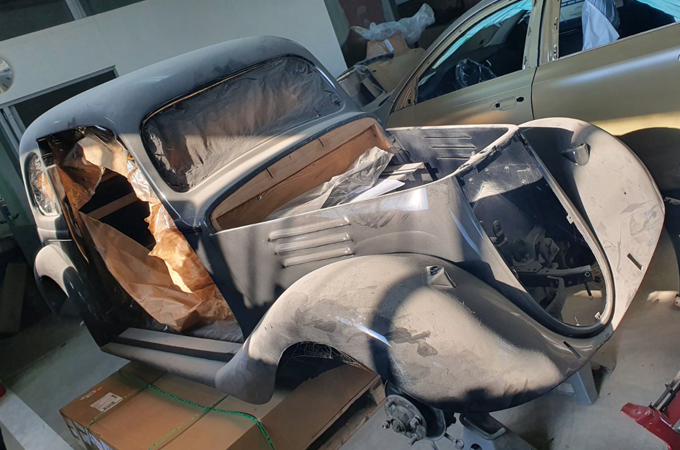
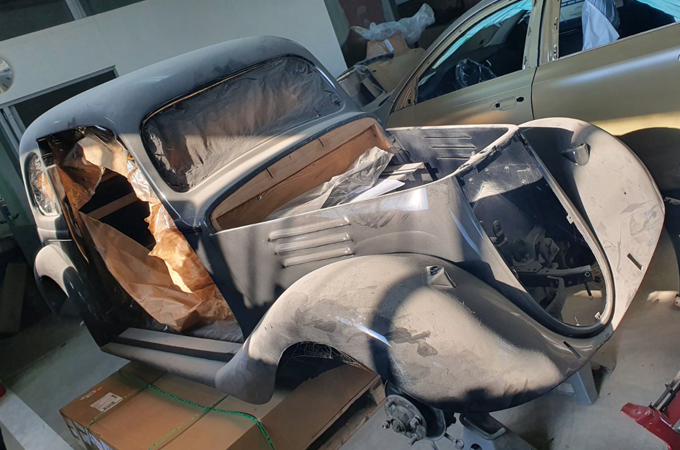
Održivost za Škodu nije samo reč. To je cilj koji inicira niz procesa u kompaniji i kod dobavljača, kako sada tako i u budućnosti
Da li ste znali da se samo deset posto plastike u svetu reciklira? Ili da u okeanima ima jedan kilogram plastičnog otpada na svaka četiri kilograma ribe – a taj paritet će se prevazići oko 2050. godine? Ima još dosta prostora za napredak. Zato je Škoda objavila svoje ciljeve i planove u ovom području: do 2030. dosledno će promovisati klimatski neutralnu mobilnost; prepoloviće emisije CO2 flote u odnosu na 2020. godinu; intenzivno je fokusirana na eMobilnost, klimatski neutralnu proizvodnju i materijale koji se mogu ponovo koristiti i reciklirati.
eMobilnost i neutralnost
ugljenika
Smer je jasan: Škoda će do 2026. imati tri nova potpuno
električna modela, a u narednim godinama biće dodato još. Do 2030. udeo potpuno
električnih vozila u evropskoj prodaji brenda trebalo bi da poraste na više od
70 posto. Češki proizvođač automobila takođe nastoji da postigne maksimalno
smanjenje emisije CO2 tokom celog proizvodnog ciklusa. Škoda proizvodni pogoni
u Indiji biće CO2 neutralni 2025. godine. Sve tri češke proizvodnje imaju isti
cilj do 2030, a jedna od njih – proizvodnja u Vrchlabí - to je postigla krajem
2020. godine.
Održiva rešenja za
sadašnja i buduća vozila
Škoda gleda i van svog dvorišta kada je u pitanju održivost.
Blisko sarađujući sa partnerima, Škoda razvija održiva tehnološka rešenja za
sadašnja i buduća vozila. To se odnosi na kupljeni materijal kao i na njegovu
proizvodnju i transport. Za proizvodnju održivih proizvoda Škoda se oslanja na
dobavljače koji prvenstveno koriste reciklirane sirovine i sirovine koje je
moguće reciklirati i imaju nisku emisiju ugljenika. Osim toga, kompanija se
uključuje u intenzivne i detaljne razgovore sa svojim partnerima o inovativnim
idejama za budućnost. Neki primeri mogu se pronaći u ovom članku.
Otpadom se takođe pažljivo upravlja u proizvodnji u Vrchlabí:
od početka 2019. sav otpad iz proizvodnog procesa reciklira se materijalno ili
termički. Druge dve fabrike u Češkoj - Mladá Boleslav i Kvasiny - rade isto od
početka 2020. godine. Održivost je takođe motivacija za inovacije, kao što je
inovacija koja omogućava farbari da nanese jedan od četiri sloja boje znatno
tanji uz zadržavanje istog kvaliteta i trajnosti. Time će se u češkim
proizvodnim pogonima uštedeti oko 720 tona boje godišnje.
Kako je
moguće uštedeti na materijalu tokom farbanja:
Ciklus održivosti
materijala
Materijali koji mogu da se recikliraju, a još bolje oni koji
su već reciklirani – to su materijali koje treba maksimalno koristiti. To se
odnosi na karoseriju, šasiju i unutrašnjost. Škoda je već postigla neverovatan
udeo materijala koji se mogu reciklirati i ponovo koristiti i koji čine više od
95 posto težine automobila.
Šta to zapravo znači: u modelu Škoda Octavia, gotovo trećina
sirovina koje se danas koriste dolazi od recikliranih materijala. Uz čelik,
aluminijum i staklo, to uključuje plastiku i izolacione materijale kao što su
obloge šasije, lukovi točkova i obloge prtljažnika. Koje će druge pogodnosti
ponuditi automobil kada dođe do kraja životnog veka? Njegovi metali se koriste
za izradu novog čelika i aluminijuma za nove delove. Otpadno staklo koristi se
za izradu novih prozora ili izolacije od stakloplastike. A plastika se koristi
u novim svakodnevnim predmetima kao što su vešalice za odeću ili posude za
cveće.
Ekološkije gume
Jedan od delova automobila gde Škoda radi na održivosti su
gume. U budućnosti će za ove delove biti moguće koristiti visok udeo održivih
materijala, a gume će se isporučivati sa FSC sertifikatom ako zadovoljavaju
stroge zahteve kvaliteta i bezbednosti. To je jedan od razloga zašto
proizvođač automobila blisko sarađuje sa svojim partnerima. Continental, na
primer, nudi gume sa većim udelom recikliranog materijala i istražuje
korišćenje prirodne gume od maslačka. Bridgestone već isporučuje lakše gume s
manjim otporom kotrljanja za Enyaq iV.
Novi elementi
enterijera
„Mono-materijale“, tj. delove koji se sastoje od samo jednog
materijala, najlakše je i najefikasnije reciklirati. Koriste se, recimo, u
unutrašnjim oblogama, vazdušnim kanalima ili kao bakarni provodnici u
kablovskim snopovima. Ovi reciklirani materijali se koriste, na primer, u
presvlakama za sedišta ili patosnicama. Zbog visokih tehničkih zahteva većina
delova novog automobila danas se izrađuje od kompozitnih materijala. Primer su
obloge vrata u modelu Octavia - polovina kompozitnog materijala izrađena je od
obnovljivih sirovina.
Jedan tradicionalni materijal za oblaganje raznih unutrašnjih
elemenata je životinjska koža. To se takođe može rešiti uključivanjem održivih
materijala. Škoda koristi ekstrakt lista masline za štavljenje kože za ponudu
modela Enyaq iV. Zavisno od modela, koža se može naći ili isključivo na
središnjem delu sedišta, ili i na upravljaču i ručici menjača i ručne kočnice. Inače,
dizajneri enterijera sve se više okreću tekstilnim presvlakama gde se tipično
koristi koža, na primer na kontrolnoj tabli. Tkanine izrađene od do sedamdeset
posto recikliranih PET boca već su dostupne za modele Enyaq iV i Karoq. One se
nakon recikliranja prerađuju u pređu. Za unutrašnje presvlake za sedišta Lodge
za model Enyaq iV, ova se pređa kombinuje sa prirodnom vunom.
Osim toga, Škoda radi na razvoju održivih materijala sa
prirodnim komponentama koji će se takođe koristiti u masovnoj proizvodnji u
budućnosti. To uključuje, na primer, vlakna od šećerne repe, koja su
nusproizvod fabrike šećera u Dobrovicama u blizini fabrike u Mladá Boleslav.
Vlakna šećerne repe koriste se za proizvodnju punila za plastične delove.
Inženjeri takođe mogu da iskoriste pulpu šećerne repe: ona se boji posebnim
postupkom kako bi se stvorili dizajnerski naglasci u enterijeru. Ali, budućnost
pripada i vlaknima srebrne trave (Miscanthus), na primer, a eksperimentiše se i
sa pirinčanom ljuskom i vlaknima konoplje, plute i kokosa.
Kišobrani i dušeci
Kao deo svoje težnje za postizanjem maksimalne održivosti, češki proizvođač automobila obraća pažnju čak i na ono što se može činiti trivijalnim detaljem. Na primer, sledeća generacija kišobrana, koji su jedan od najpoznatijih Simply Clever elemenata u unutrašnjosti automobila iz Mladá Boleslav, biće u potpunosti izrađena od recikliranih materijala, a njihova ručka će biti izrađena od vlakana konoplje. Ako kišobran pukne, moći će da se popravi i ponovo koristi. A evo još jednog primera uspešne i inovativne saradnje, ovaj put sa Trèves Grupom: kako bi nabavili materijal za zvučnu izolaciju automobila, ova multinacionalna grupa čisti, dezinfikuje i usitnjava stare dušeke koji bi inače završili na deponiji.
Komentari(0)